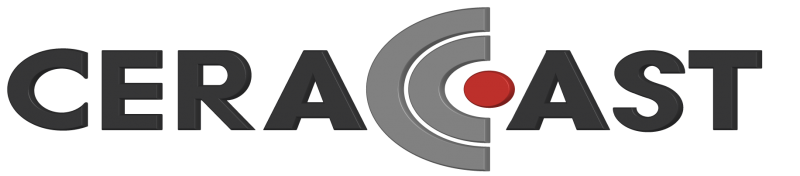
CERACASTTM is a castable with superb physical and chemical properties that sets itself apart by its bonding system. Based on ultra-packing particle properties CERACASTTM castables shows a unique combination of high wear resistance, thermal resistance and mechanical. Different formulations and aggregates determine the properties for each grade. CERACASTTM can easily be mixed, cast, and shaped. Different grades are available for different application systems: casting, trowelled, self-flow ing, gunite. Supplied as parts, CERACASTTM is cast in a wide range of shapes and sizes with the finished products exhibiting exceptional dimensional stability. Different grades can be used within a wide range of temperatures and applications exposed to thermal shock conditions in industries like aluminum, cement and power plant, mining, and other industrial areas with severe abrasion/erosion.
CERACAST A
Castable with good thermal and electrical insulating properties. Widely used in aluminum, ferroalloys, mining, cement, and steel industries.
Available version :
Castable – Self-flowing – SprayCast – Trowallable
CERACAST SYFLEX
A Silicon carbide castables with extreme abrasion resistance, high thermal conductivity and resistance, and excellent thermal shock- and alkali resistance properties. Castables can be used in all industries where abrasion and thermal shock in the hot and extreme abrasive environment, as well as areas in contact with molten metal HTS type, has a maximum service temperature of 1500 °C
Castable – Self-flowing – Trowallable Shaped
CERACAST ALSIC
Material based on bauxite and silicon carbide, good strength, good wear resistance, low heat conductivity, good abrasion resistance, and the ability to withstand thermal shock.
Castable – Self-flowing – Trowallable – Shaped
CERACAST ZYFLEX
CERACAST FS is based on fused silica material with very low thermal expansion and thermal conductivity. This material is naturally non-wetting and formulated especially for use with high silicon alloys, typically foundry alloys.
Version available: Shaped
CERACAST WFA
CERACAST WFA is based on white fuse alumina. This dense castable possesses low thermal conductivity and stands out for high temperature and chemical attack resistance.
Castable – Self-flowing – Trowallable – Shaped
CERACAST modern refractory concept for the aluminium industry exploit the advantage of shaped products and provide wear and abrasion solutions for components, flooring or other surface exposed to molten aluminium.
Prefabricated components, employed for the most part in aluminum smelting and holding furnaces, provide the highest standard of material quality and production process accuracy.
CERACAST offers a comprehensive range of precast systems including
- Door Frames
- Ladles and Bottoms
- Submerged Cones
- Complete Furnaces
- Furnace Ramps
- Skimming Tools
- Floor Tiles
- Runners
- Dossing Cup
- Piping
CERACAST standard products and prefab find application in several processes area of the Cement industry where it is required resistance towards high wear hot temperatures, chemical attacks, and mechanical stress.
Shaped CERACAST
- Vault brick
- Nose Ring
- Air Blasters
- Lining Slabs
- TAD
- Inlet lip
- Tiles
Hard facing solution for:
- Cement grinding raw meal
- Coal separator
- Outlet chute
- Dust collecting cyclones
- Pipes for dust collecting and cooling
- Hopper
- Fly ash
- Pipe and Duct linings
For better machinery and abrasion resistance, CERACAST provides wear protection for thermal coal power plants, lignite, biomass or recycling waste, sludge, facing severe abrasion phenomena.
CERACAST provide a safe and cost-saving solution for the following equipment:
Bunkers
- Channels
- Chutes
- Cyclones
- Deviation hoods
- Dust collecting ducts
- Hoppers
Conveying
- Pipes and pipe bends
- Separators
- Silos
Wear is an inevitable effect of handling abrasive materials in processing lines. Wear cannot be avoided, but it can be controlled by protecting exposed parts of your plant with a wear resistance lining.
CERACAST offers reliable wear protection and wears resistance solutions in all plant components and production areas. The goal is to prevent the need for unscheduled repairs and to avoid production downtime.
CERACAST Wear Protection extends the lifetime and security of equipment in steel plants:
- Blast furnace hoppers
- Chutes
- Crash decks
- Dedusting cyclones and ducts
- EP ducts
- Fan casing feed chutes
- Granulation systems • Injection and manifold pipes
- Material and Mill hoppers • Roll feeders
Sinter hoppers
- Slurry pipes
CERACAST wear protection solutions reduce operating costs in mining applications by extending service life, reducing personnel costs, and minimizing downtime.
Protective Ceracast linings can be used to extend the lifetime of:
- Chutes
- Hoppers
- Conveyors
- Fan housings
- Cyclones
- Piping
- Feeders mining and mineral processing of quartz, coal, iron, and precious metals.
- Dedusting system
- Separators
- Slurry pipeline
CERACAST extend the lifetime and security of equipment in chemical plants:
- Conveying
- Mills
- Separators
- Mixer
- Cyclones
- Tanks
Glassworks
Quartz sand in glass production requires good industrial wear protection for the pipelines used to fill the silos and feed the tanks. The processing and conveying equipment used in recycling old glass also has to be protected.
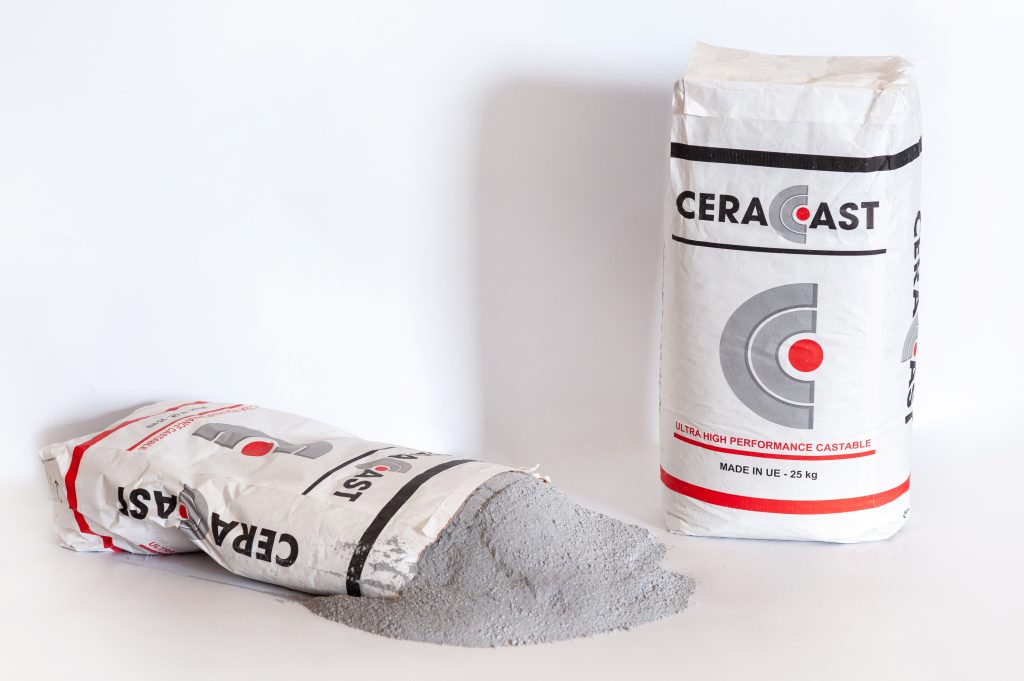